Un des textes gagnants du Concours de vulgarisation scientifique 2019
Petit mais costaud : un minirésonateur qui fait le maximum
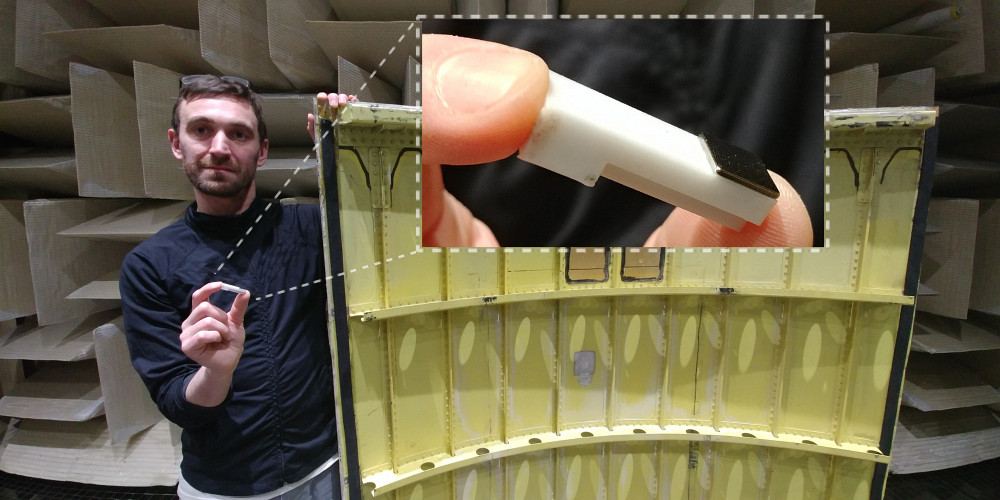
Le chercheur Olivier Robin tenant le panneau de fuselage testé et un résonateur dans la main
Photo : Olivier Robin
Une vitre qui se met à vibrer quand un camion passe dans la rue, le lave-linge qui fait plus de bruit durant l’essorage, le fuselage d’un avion, la carrosserie d’une automobile, les murs d’un local : vous connaissez tous des exemples de structures qui vibrent et transmettent du bruit.
Ces structures, on les voudrait toujours plus fines, légères et rigides en utilisant des matériaux composites ou des alliages ultra-optimisés. Problème : plus une structure est légère et rigide, moins elle est performante en termes d’isolation acoustique. Il faut alors souvent l’améliorer en y ajoutant des traitements absorbants, ce qui est particulièrement contraignant pour les basses fréquences, les sons graves. En effet, plus la fréquence est basse, plus le traitement doit être épais, lourd et coûteux. Les manufacturiers souhaitent généralement l’inverse, soit réduire le poids et le coût.
Plus avec moins ?
Alors réduire le bruit avec peu, c’est mission impossible ? Non. Des chercheurs de l'Université de Sherbrooke et de l’École centrale de Lyon ont atteint cet objectif pour un panneau de fuselage d’avion [voir photo]. Autour d’une fréquence de 680 Hz, ce panneau de presque 3 m2 montre une perte importante de son isolation acoustique, et seul un espace très réduit est disponible pour intégrer un traitement. Pour trouver une solution originale à ce problème, l’équipe a d’abord choisi de raisonner selon les principes que le minimum peut faire le maximum et que l’union fait la force. Et a ensuite choisi de résonner : si l’on frappe à l’extrémité d’une règle fixée sur le bord d’une table, elle vibre à sa fréquence de résonance qui dépend surtout de ses dimensions et du matériau avec lequel elle est construite. Si on place ce résonateur sur une source vibrant à la même fréquence, il va absorber et dissiper de l’énergie.
La forêt de bonsaïs vibrants
Voilà l’idée : remplacer les traitements encombrants et lourds par une forêt de résonateurs miniaturisés. L’impression 3D a permis de réaliser des prototypes de la taille de votre pouce, chacun pesant moins de trois grammes. Sur le panneau de fuselage, plus de 200 résonateurs ont été répartis pour atteindre un effet maximal. Les tests en laboratoire montrent une isolation acoustique dix fois plus importante dans la zone qui était problématique, maintenant une de celles où la performance est la meilleure !
Vu ses dimensions, le minirésonateur peut se glisser presque partout, et l’ajout de masse est très faible, moins de 5 % pour le panneau étudié. Le nombre de résonateurs et leur fréquence sont facilement ajustables suivant la réduction de bruit souhaitée pour une application. On peut en imaginer sous le capot d’une automobile, dans les parois des appareils ménagers comme les lave-vaisselle ou encore dans les encoffrements autour des machines bruyantes dont les performances sont souvent limitées par la place disponible. Et vous, quel objet bruyant du quotidien aimeriez-vous améliorer ?
Un problème de taille
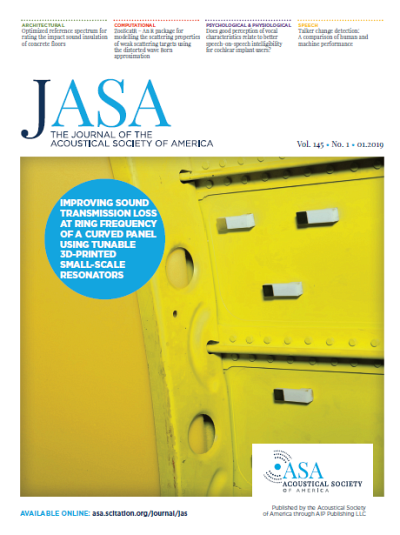
Photo : Image
Mais finalement, pourquoi les traitements insonorisants doivent théoriquement être épais ? C’est une question de rapport à la longueur d’onde acoustique, la dimension spatiale de l’onde que l’on veut absorber. Pour être pleinement efficace, le traitement doit avoir une épaisseur au moins égale à un quart de cette dimension. Un exemple concret : à une fréquence de 680 Hz, proche du son typique d’un klaxon, la longueur d’onde acoustique vaut 50 cm, donc l’épaisseur idéale de matériau absorbant pour atténuer ce bruit serait de 12,5 cm. C’est 1 cm de plus que la hauteur d’une canette de soda, et c’est déjà beaucoup.
À propos d'Olivier Robin
Olivier Robin est professionnel de recherche au sein du Groupe d’acoustique de l’Université de Sherbrooke (GAUS), au Département de génie mécanique de la Faculté de génie. Il travaille principalement sur des problématiques de vibroacoustique appliquée dans le cas de véhicules, du bâtiment, des alarmes sonores et également sur le développement des techniques de mesure dans ces domaines.
À propos du concours
L’Université de Sherbrooke tient annuellement le Concours de vulgarisation scientifique, dont les objectifs sont de stimuler des vocations en vulgarisation scientifique et d’augmenter le rayonnement des travaux de recherche qui s’effectuent à l’Université, qu’ils soient de nature fondamentale ou appliquée.