Innovations technologiques
Construire un hôtel comme des blocs Lego

Photo : Maxime Picard, collaborateur
Et si l’érection des 10 étages d’un immeuble hôtelier pouvait se réaliser dorénavant en moins de 5 jours? Avec les délais actuels connus dans le secteur de la construction, cette nouvelle possibilité s’avère plus qu’intéressante. Quand un chercheur en structure s’allie avec une entreprise spécialisée en construction modulaire, on ne redéfinit rien de moins que le futur de la construction immobilière.
Les projets de construction modulaire existent depuis plusieurs années, principalement pour des bâtiments de faible hauteur : écoles, hôpitaux, camps miniers, résidences d’habitation. Mais un nouvel élément s’est récemment invité dans l’équation : l’acier. Les bâtiments modulaires existants sont principalement en bois. Réussir à ériger une structure modulaire de dix étages qui résiste aux différentes charges, comme le vent et les tremblements de terre, demandait des adaptations au niveau structural. Charles-Philippe Lamarche, professeur au Département de génie civil et de génie du bâtiment, a travaillé au cours des quatre dernières années avec son équipe, de concert avec l’entreprise RCM Solutions Modulaires, pour livrer la plus haute structure modulaire en acier au Canada : le Holiday Inn de Gatineau. Une structure de 12 étages.
L’acier permet d’élever plus haut les structures modulaires, principalement grâce à sa très haute résistance. L’innovation réside principalement dans les connexions intermodulaires, qui permettent aux modules de s’imbriquer un sur l’autre de façon optimale. La connectivité est assurée par un mécanisme mâle-femelle reliant les segments de colonne des modules superposés. Comme des blocs Lego.
Charles-Philippe Lamarche
Ehsan Bazarchi, étudiant au doctorat sous la direction de Charles-Philippe et de la professeure Nathalie Roy, a d'ailleurs remporté le prix de la meilleure présentation en mai dernier dans le cadre du colloque annuel du Centre d'études interuniversitaire des structures sous charges extrêmes (CEISCE), à Polytechnique Montréal, pour sa présentation intitulée « Le plus haut bâtiment modulaire au Canada : développement de concepts structuraux pour résister aux charges sismiques, de vent et de transport. »
Les avantages du modulaire
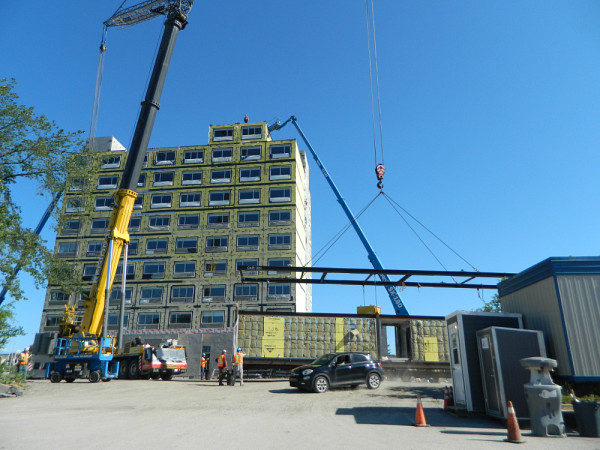
Photo : Fournie
Un autre aspect innovant qui a été mis de l’avant dans le cadre du projet de recherche réside dans le fait que, au lieu de transporter des modules d’environ 30 pieds, comme c’est souvent le cas, le groupe de recherche et l’entreprise ont conçu des modules plus grands, soit de la longueur maximale pouvant circuler sur nos routes : 66 pieds! Du jamais vu dans l’industrie. La participation de M. Serge Parent, professeur associé au Département de génie civil et de génie du bâtiment, a été un atout important dans cette phase du projet. Chaque module comporte deux chambres d’hôtel avec salles de bain et un corridor, et il s’installe en moins de 20 minutes. L’idée est de pouvoir réduire au maximum les heures travaillées en chantier et de pouvoir monter la structure très rapidement une fois les modules livrés.
Toujours dans l’exemple hôtelier, la finition interne des modules est déjà faite. Les lits, machines à café, bureaux, toilettes, bains, douches, comptoirs, tout est déjà en place. Et il y a plusieurs autres avantages dans une telle structure modulaire. Comme les modules sont construits directement en usine puis transportés sur les sites de construction, on a besoin de moins de main-d’œuvre, l’environnement est mieux contrôlé, les produits sont standardisés, et le temps de construction diminue. L'érection du bâtiment se fait beaucoup plus rapidement une fois sur le site, et il y a beaucoup moins de déchets produits, moins de nuisances sonores environnantes et moins de trafic routier dans le voisinage.
Charles-Philippe Lamarche
Du béton dans certaines connexions
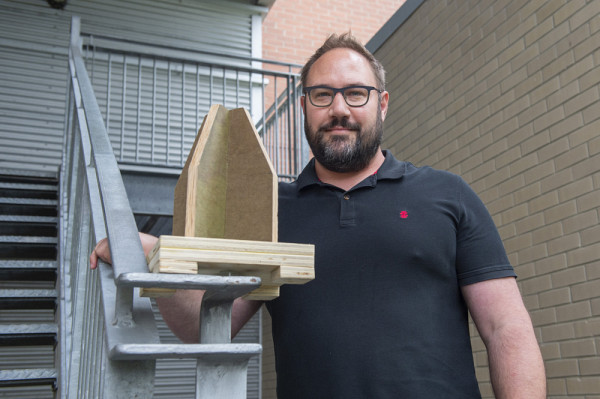
Photo : Maxime Picard, collaborateur
Dans le concept mis de l’avant, les modules sont empilés les uns sur les autres verticalement, et les colonnes ne sont pas attachées dans le sens vertical. Pour ce type de construction modulaire, on peut, comme pour une chaise qui est difficile à tirer lorsqu’il y a du poids dessus, se fier aux charges gravitaires provenant des étages supérieurs et à la friction entre les éléments pour résister aux charges latérales (vent, séismes). Cependant, lorsqu’on arrive en haut du bâtiment, il n’y a pas assez de friction pour prévenir de potentiels glissements horizontaux au niveau des derniers étages.
D’un point de vue sécuritaire, c’est correct, affirme le professeur, puisque les glissements sont petits et limités par la tolérance entre les pièces dans les connecteurs. Cependant, il est possible que certains glissements horizontaux puissent survenir entre les modules dans les étages supérieurs supportant moins de poids. Ces glissements pourraient causer certains inconforts aux utilisateurs sous des charges de vent , comme des grincements, des craquements. Pour pallier ce problème, les spécialistes du béton du Département ont été mis à contribution : le professeur Richard Gagné et Audrey Albert, étudiante à la maîtrise, ont développé un coulis expansif qui, une fois injecté dans les connexions, prend de l’expansion et vient empêcher tout mouvement dans les connecteurs situés aux étages supérieurs.
Pour le moment, le concept modulaire inclut des murs de refend en béton armé comme système de reprise des charges latérales. Depuis janvier, Charles-Philippe et son équipe travaillent avec RCM Solutions Modulaires et la firme d’ingénierie Côté-Jean et Associés, un nouveau partenaire, dans le cadre de la deuxième phase du projet pour que des systèmes de reprise des charges latérales en acier soient directement intégrés dans les modules. Cette nouvelle technologie permettra de préfabriquer entièrement la structure en usine et ainsi d'augmenter davantage la vitesse de construction et la rentabilité des projets.
Ce qui me motive dans ces projets-là, exprime le professeur, c’est que ce sont des choses qui n’ont jamais été faites, ou peu faites, dans l’industrie. Une entreprise te propose une idée de projet qui doit être réalisé dans un temps donné et qui n’existe pas encore. C’est hyper motivant. On voit tout ça prendre forme au fur et à mesure que le projet avance. Pour les étudiants et étudiantes, c’est vraiment gratifiant aussi. Une super expérience!
Tabliers métalliques inédits
En parallèle, Charles-Philippe poursuit aussi des recherches avec une entreprise de la Beauce spécialisée dans les bâtiments d’acier, Métal Sartigan. On touche encore à l’acier, mais cette fois l’innovation se trouve dans les tabliers métalliques, constituant structural important des toits et planchers, auxquels on a ajouté des raidisseurs. Une autre nouveauté que l’on ne voit pas souvent en Amérique du Nord.
L’innovation ici se trouve essentiellement dans la profondeur des tabliers, explique le professeur Lamarche. Normalement, on parle de 75 mm de profondeur et moins. Dans ce projet, on a un tablier de 100 mm de profondeur qui été développé sur mesure. Ces éléments structuraux sont plutôt complexes à concevoir à cause de certains phénomènes d’instabilité qui ne sont pas rencontrés dans les tabliers conventionnels. Pour pallier ces instabilités, des raidisseurs doivent être ajoutés.
La phase initiale de conception du projet été lancé à Polytechnique Montréal par le professeur Robert Tremblay et Ali Davaran, professionnel de recherche. Depuis les trois dernières années, un projet de recherche faisant suite aux travaux effectués à Polytechnique a été amorcé à l’Université de Sherbrooke pour caractériser les propriétés du tablier par des essais à grande échelle. L'équipe sur place travaille à développer de nouvelles équations de conception qui seront adoptées éventuellement dans les normes nord-américaines pour des tabliers profonds comme celui étudié.
On est présentement dans la troisième année du projet, poursuit le professeur Lamarche, et on comprend mieux le comportement du tablier sous charges verticales (gravité) et horizontales (vent, séisme). Les essais grandeur nature réalisés en laboratoire et les modélisations numériques de pointe ont permis de livrer un premier bâtiment avec ce nouveau tablier à l’automne 2021.
Avec cette nouvelle technologie, on peut espacer les poutrelles de toit de 12 pieds au lieu de 6 ou 8 pieds. Ceci a pour effet de significativement réduire la quantité de poutrelles en acier nécessaire étant donné la résistance accrue du tablier. Pour un bâtiment industriel ou commercial, cela réduit significativement le tonnage d’acier, et l’érection de la structure est plus rapide : économie de temps et de matériaux.